- 版权所有© 2003-2021范吉仿真工程技术公司. 沪ICP备08111035号.
- 上海市徐汇区斜土路2601号嘉汇广场T2-26F,邮编:200030
- 电话:+86-21-51097827 传真:+86-21-51096351
FEAPro Engineering supports our Integrated Product Teams with structural design or analysis, depending on project requirements. Our structural engineers design tools and use best-practice methods to ensure the accuracy of our analyses while compressing schedules.
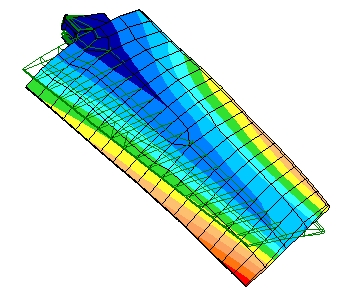
- -Thermal/stress Analysis
- - Steady state or transient
- - Linear elastic or plasticity
- - Contact Analysis
- -Dynamic Analysis
- - Stage vibration
- - Damper design
- - Forced response
- - Acoustics
- - FOD/DOD simulation
- -Lifetime Prediction and Validation
- - Mission analysis
- - Creep analysis
-
- Fatigue (LCF/HCF/TMF) and fracture analysis
- -Preliminary Vibration Analysis
- - Preliminary neck length
- - Airfoil taper
- - Frequency margins
- - Flutter margin
- - Damping parameters
- - Airfoil 2D temperatures
- - Thermal strain analysis
- - Damper shape optimization
- - Airfoil stacking
- -3D Design Analysis
- - Metal temperatures
- - Full load stresses
- - LCF life
- - Goodman diagrams
- - Fracture screening
- - Damper performance
Ask for a specified software solution:
please click on send us a feedback
Thermal Analysis
Engine Cooling
With the growth of turbo technologies under hood temperatures are rising and the cooling system is of growing importance. Cooling in the vehicle cockpit is rapidly becoming a standard feature in passenger vehicles. Trelleborg’s polymer product portfolio can be found throughout these systems.
Packaging the engine cooling system is indeed a major driver of innovation. Engine cooling systems must fit into ever smaller spaces under the bonnet.
Given the pressure on supplier to squeeze higher performing products and systems into a smaller space under the bonnet, radiators have gradually become smaller in size. Reducing pollution and fuel consumption, and enhancing passenger comfort are asked to realize. Numerical simulation and physical testing will help engineers to challenge the new record.
FEAPro Engineering provide an integrate methodology to help engineers to solve engine cooling problems by numerical simulation and physical testing. You could fi11nd out more about the solution by click the following links to applying a wonderful solution.
Ask for a specified software solution:
please click on send us a feedback
Electronic Cooling
FEAPro Engineering provide an integrated solution, used for thermal management by design engineers in the electronics industry. By predicting air flow and heat transfer at the component-level, board-level, or cabinet-level, Our solution improves design performance, reduces the need for physical prototyping, and cuts time-to-market.
Ask for a specified software solution:
please click on send us a feedback
Space Thermal Radiation Solution
FEAPro Engineering provide a comprehensive finite-difference, lumped parameter (circuit or network analogy) tool for heat transfer design analysis and fluid flow analysis in complex systems.
For years, these methods has provided users with the most proven heat transfer and fluid flow design and analysis software in the aerospace industry.
Our solution is a comprehensive, generalized tool for simulating complex thermal/fluid systems such as those found in the electronics, automotive, petrochemical, turbo-machine, and aerospace industries. The solution has proven itself repeatedly for several decades.
It saves time and money by making the design process faster and easier, letting you gain a better understanding of your complex system. You control what is important and how to get the answer to your design performance questions using the most efficient approach.
Ask for a specified software solution:
please click on send us a feedback
CFD (Computational Fluid Dynamics)
FEAPro Engineering provides a fluid dynamic (CFD) simulation environment based on the stabilized Finite Element Method. The solution works with number of different turbulence models and sophisticated tools for simulating problems of species advection, heat transfer in fluids and solids, as well as free surface among others. It also includes fully integrated pre/post-processing modules.
FEAPro Engineering’s solution is highly flexible in defining physical properties of the model, boundary conditions, through user-defined functions that can make it a tool with large variety of applications. Moreover, The advanced solution includes wizard-type utilities to make analyses definitions fast and easy to do. It also can be easily adapted to specific needs allowing a simple and automated analysis process.
Advantages
-
Using FIC/FEM method nake it possible to solve CFD and multiphysics problems.
- Solve heat transfer problems in both fluid and solid domains
- Solve fluid flow including turbulence phenomena, advection of species, structural mechanics and Free Surface (NAVAL and ODDLS modules) problems
- It is also possible to configure additional user defined partial differential equations (PDE) solvers and couple the new variables with any of the other problems
- ALEMESH module can be used to simulate problems where mesh deformation (i.e. body movement) may occur.
- Tcl interface enabling users to enhance simulations without recourse to external compiled subroutines.
- All in one solution: fully integrated and the complete environment is used as one single program.
Applications
-
Analysis of loads on buildings and other structures
- Ventilation and refrigeration systems simulation
- Analyses of transport and dispersion phenomena of contaminating substances
- Industrial flows simulation
- Determination and analyses of fluid separation phenomena
- Biologic flows analyses
- Fluid noise, cavitations and turbulence phenomena determination and analysis
- Heat transfer analyses in fluids and solids
- Vibrations frequency evaluation
- Pressure loss calculation in tubes and valves
- Forms optimization
Ask for a specified software solution:
please click on send us a feedback